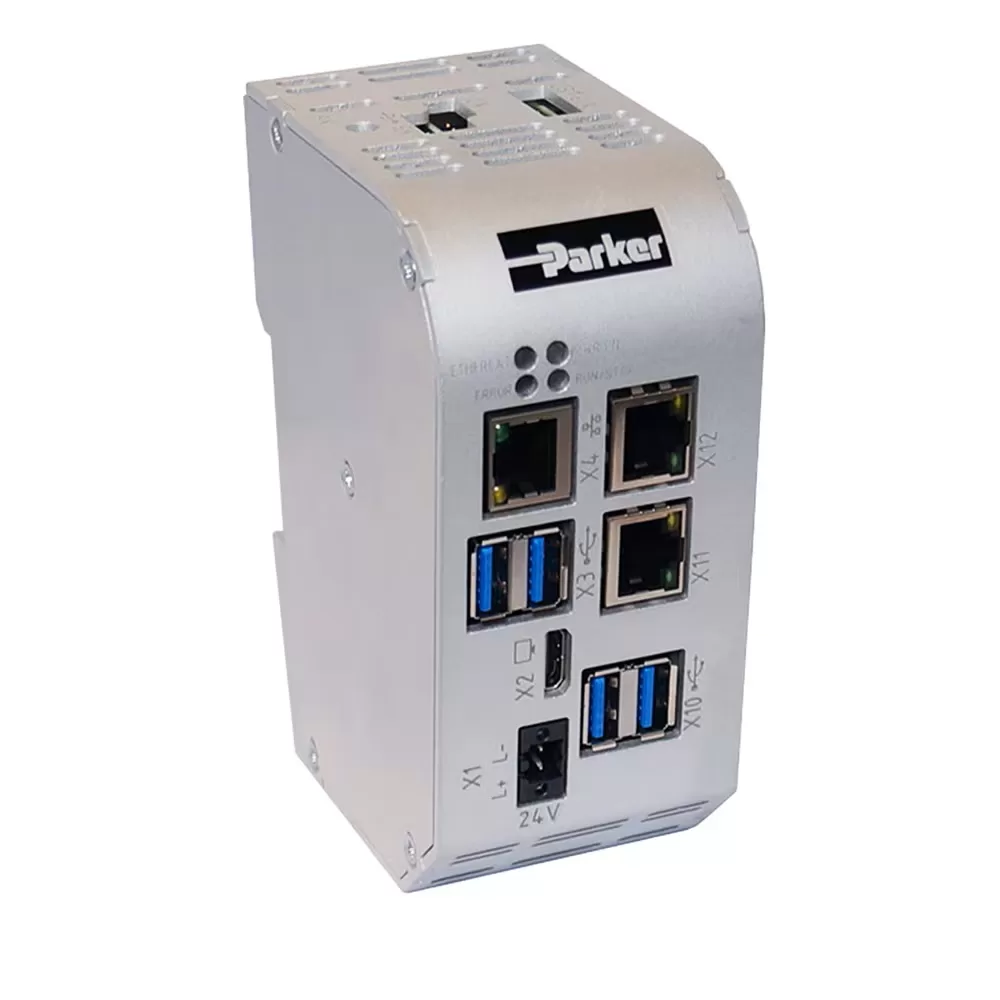
Parker Automation Controller – PAC
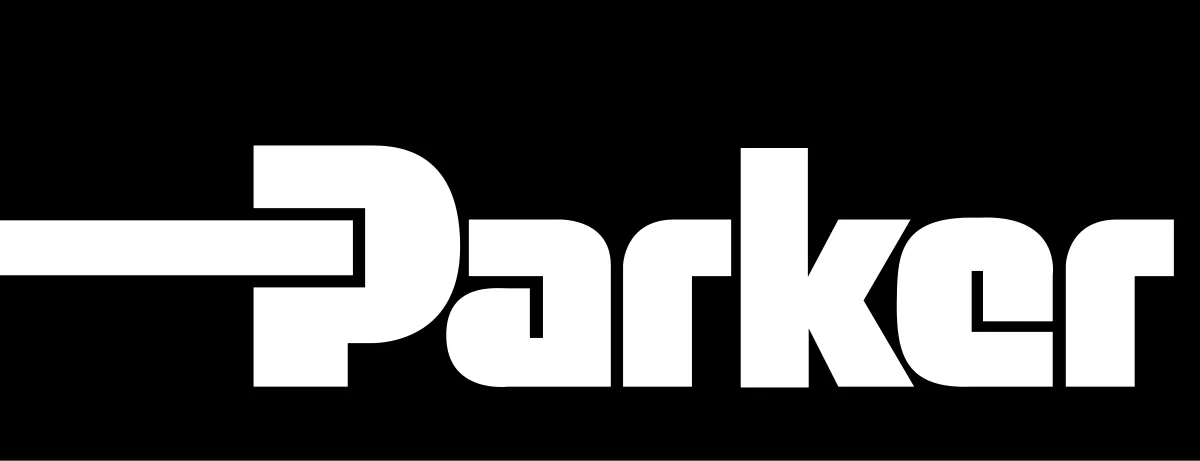
Parker Hannifin delivers precision motion and control solutions, enabling advanced automation, improved efficiency, and optimized performance across industrial and aerospace applications.
The Parker Automation Controller (PAC) is a programmable controller based on the IEC 61131-3 & PLCopen motion standards. It combines machine logic, real-time motion control & visualization into a standard fan-less & easily mountable din rail solution.
• Seamless integration with existing plant networks enhances machine productivity.
• Standard onboard communication protocols: OPC UA Server, EtherCAT, Ethernet/IP, PROFINET.
• Quick and easy commissioning with advanced debugging tools and simulation runtime.
• Faster code generation & reuse using IEC61131-3 programming languages & PLCopen function blocks.
• High modularity for flexible machine design.
• Compatible with 3rd party devices via Modular I/O & communication interfaces.
• Industrial-grade durability with removable storage, fan-less operation, and no moving parts.
When starting a machine controller project, In-Position Technologies engineers start by reviewing the key requirements to determine the optimum machine controller for the job. They perform all necessary engineering calculations to make sure the machine controller performs as required, within customer specification, and without unnecessary cost.
To ensure a machine controller fits the customer’s requirements, In-Position Technologies engineers review:
• System Size
• Functionally and Flexibility in Programing
• Performance
• Connectivity
• Security
• Compatibility with external controllers, drives and third-party machines.
When ordering a Parker Automation Controller as a part of a full system, IP Tech engineers review the solution to ensure:
• All parts and accessories necessary for a complete working solution are included
• All components have been checked and verified to work together as a system
• The selected components will perform as required by the project specifications