
Sensaria Customer Story
Our work with Sensaria
Sensaria is a premier print-on-demand wall décor manufacturer producing custom canvas photos, framed art, and metal prints. They are headquartered in Longmont CO but have manufacturing facilities across the US. Sensaria is well known for premium canvas gallery products and produces tens of thousands of units per day.
Within canvas wrap production, one of the most tedious and erroneous processes is lamination. Traditionally, it takes several workers to line up the printed canvas on an adhesive backing. It can take numerous attempts to ensure that the image is centered when folded over a frame. To address the need to ramp up and ramp down labor during their busy season – Sensaria has historically resorted to temp agencies to fulfill their labor needs. Hiring and training temp workers was not only expensive but increased quality issues and it became clear Sensaria needed an automated solution.
The In-Position Technologies team worked closely with Sensaria engineering to develop a cobot solution that would automate this lamination process. The process requires the printed canvas to be precisely picked from a stack and placed onto an adhesive backing. However, several challenges had to be solved to successfully automate the application.
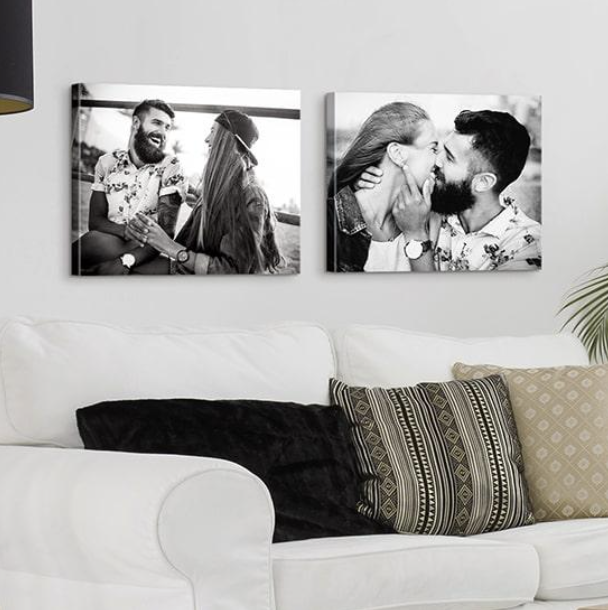
The first challenge was picking the canvas without inducing pucker marks when placed on the adhesive. IPTech was able to test several different gripper technologies including vacuum, adhesive force (Van Der Waals), and non-contact grippers. We successfully concluded a special Bernoulli style gripper would pick the canvas material without inducing marks.
The second challenge was picking from a stack that wasn’t perfectly positioned or flat. Although the stacked canvases are in the same general orientation, they have slightly different XY positions and rotations. Each canvas may also have slight differences in thickness, which could result in a changing pick height. With a requirement to place the adhesive backing to within +/- 0.015’’, it would be critical to always pick from a known position.
The IPTech team helped integrate the Universal Robot with Datalogic P2x Smart cameras so that the robot could pick the top canvas precisely off a corner registration mark. In addition, the Universal Robot’s integrated force torque sensor was used to press against the stack with force to account for the ever-changing stack Z height. The UR’s force torque sensor would also release compliance in RX and RY to allow the robot to repeatably adhere to the canvas in case the top of the stack was not completely flat.
With the application challenges solved, Sensaria was able to internally develop custom cells to handle the lamination of several high-volume canvas sizes. The cells were developed with human interaction for loading adhesive backing, while the robot handled the rest of the process. Overall, each of these cells reduced two temporary labor operators per machine per shift. Lamination errors cut in half and the processing time was reduced by an average of two seconds per canvas.